I've recently completely cleared out the studio and found my fake books: I'm not a huge jazz fan, but the complexity of the music (in comparison to other styles) and the way the books are laid out (just melody and chords) is a great study tool for "knowing the chords".
Historically theory isn't my strong suit: I remember a disgusted sax player who couldn't understand why I couldn't play through changes in a more complex song, just by knowing the chords. The truth is, like lot of self-taught players, I've done it all by ear, really: I can learn basslines from the dots but I don't have a cerebral grounding in chord theory and knowing the language, so to speak.
I plan to start stretching myself in this department. Today I just started with a youtube video of a backing for Donna Lee at http://youtu.be/fVOTUXfqhhE and the fake book entry: Listening to the backing, I know where the song is having learned the Jaco solo: but playing the bassline through the changes? Once again - I'm not fluent, not fluid: I don't yet understand how this is done. I can see a lot of work ahead, and the thing is to break the blank sheet anxiety and get stuck in with the modern resources at hand.
Wish me luck. What are you shedding with?
P.S. Tomorrow is Rikkers pick-up day!! I suspect the bass is currently on the front of the Rikkers stand, where it's picking up some attention :-)
Daily happenings in a UK Bass Player's tiny tiny Gig fuelled world...
Saturday, March 07, 2015
Tuesday, March 03, 2015
Rikkers Build, Part 5: THE FINAL STRETCH….!
Background - I commissioned a custom Olive-faced 5-string bass from Rikkers in Holland - 15 years or so after first considering a custom bass. The experience has been an education, and a great experience (I can recommend Rikkers), so I thought I'd properly document it.
The other parts:
Nice to see the guys sign the bass on the inside as well as showing their quality on the outside!

Getting the pickups fixed in place is an interesting job, and wiring her up (for 18v of wicked overhead via the OBP-3 preamp) takes a while, and needs Jacco the Wiring God and his Goggles of Extreme Precision.
Marvel at his prowess in this video!
The wiring job looks excellent – we’re well screened here. I like the way the twin 9v batteries have their own little compartment: no way to damage electronics if they broke free, because they can’t!

Ferdinand worked his magic on the frets (stainless steel – they need some work, a set of files gets used up!)

And so, we reach the final shots – and my new beauty emerges for her closeups, Mr DeVille.
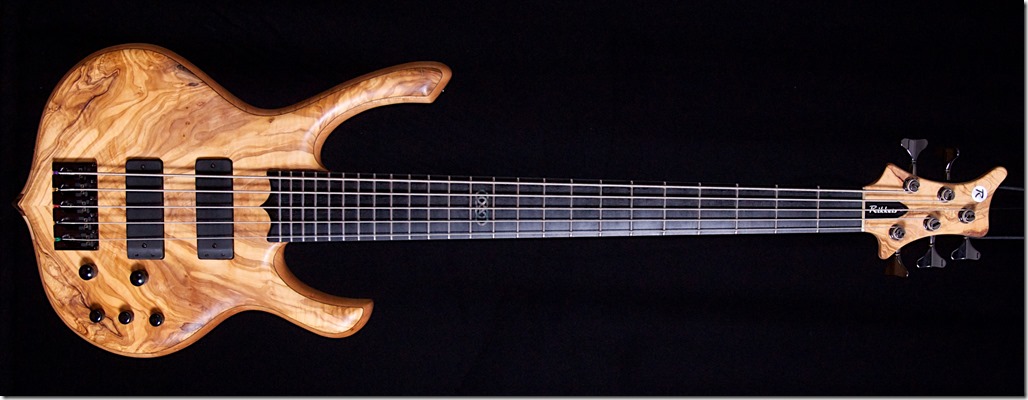

I’m booking the train tickets for Sunday TONIGHT!
The other parts:
- Commissioning the bass: How I decided what to do
- Part 1: Choosing the components
- Part 2: Early progress - the shapes emerge
- Part 3: Ferdinand works the wood.
- Part 4: The bass visualised, and “The Inlay”
Nice to see the guys sign the bass on the inside as well as showing their quality on the outside!
Getting the pickups fixed in place is an interesting job, and wiring her up (for 18v of wicked overhead via the OBP-3 preamp) takes a while, and needs Jacco the Wiring God and his Goggles of Extreme Precision.
Marvel at his prowess in this video!
The wiring job looks excellent – we’re well screened here. I like the way the twin 9v batteries have their own little compartment: no way to damage electronics if they broke free, because they can’t!
Ferdinand worked his magic on the frets (stainless steel – they need some work, a set of files gets used up!)
And so, we reach the final shots – and my new beauty emerges for her closeups, Mr DeVille.
The Bass.
I’m booking the train tickets for Sunday TONIGHT!
Monday, March 02, 2015
Rikkers build, Part 4: The Bass Emerges (and "The Inlay")
Background - I commissioned a custom Olive-faced 5-string bass from Rikkers in Holland - 15 years or so after first considering a custom bass. The experience has been an education, and a great experience (I can recommend Rikkers), so I thought I'd properly document it.
The other parts:
Recap:


I figured something around the middle of that picture would be good: done in abalone, with a bit of sparkle. Ferdinand agreed, and I sent the URL of the site across. We worked through this early on, just after settling on the materials for the build.
The build progressed nicely: we got to this stage:

And I was getting pretty excited: but then.... argh! The inlays are delayed, so we have to come up with a rapid solution (this happened a week ago last Saturday: with 2 weeks to go!!!)... so I start looking for images I can use. I measured up a different 5-string with similar spacing, and decided 40 x 15mm seems about right. We have another Facetime session, and Ferdinand tells me he knows some guys who have a computer-controlled CNC machine, and he shows me a selection of abalone which the inlay could be made out of. I'm intrigued about what might be possible, and want to keep the core idea of a celtic band.
I'm searching for celtic bands, and I find things like

which is pretty good. I filled in the shape to see how it might look, white-on-black: it wasn't bad, but still not great. And besides, with my geek hat on, I know the computer CNC guys are going to want something which isn't a JPG - they're going to want a vector format (see, I can geek!).
I hunt around and find this: Now granted, this looks pretty pixelated, but... it's an adobe illustrator file - a vector format! This could be an ideal way to get things moving quickly…

I tell Ferdinand the bottom one is preferable: I didn't twig at the time that it was a pair of infinity signs: it's a nice figure, and it scales to 15x40 well.
Anyway, I hear back from Ferdinand a couple of days later: The CNC guys were able to rout out the shape nicely, and he then engraved the piece and added black lines to give it the 3-D over/under look - and see the result!

... and when the light hits it right!!!

And finally - she's got a full set of stainless steel frets!

These are a little more expensive - Ferdinand tells me he uses an entire set of files because they're so hard: this is exactly why I wanted to specify the materials though, longevity and a trouble-free bass!
I did a little editing on my iPad to make a backdrop out of it - you can really see the beautiful work here: the CNC guys made a fine piece, and Ferdinand's engraving has absolutely made the inlay: it's just stunning!

This last show is the latest one I've got: I've seen her in one last facetime session, last friday, where Jacco (the God of Wiring, tremble in his Mighty Presence!) and I discussed how the controls would work: a great chat, where the flexibility of tone was paramount - I'm going for the switchbucker pickups, so I want to be able to get as many tones as possible. The recent work I've done on basses with OBP-3 was on basses which were modded, and already had a set layout: this meant stacked pots and blend controls.
Jacco and Ferdinand were kind enough to recommend twin volume pots for the 2 pickups: this bass has a good sized space for 5 controls!
So our final control layout is 2 above, 3 below: we have
- bridge pickup (with push/pull for passive - yay!), neck pickup as 2 separate controls
- bass, mid (with push/pull for the switchable mid on the OBP-3), treble.
That brings us up to date: My next post will be the final build blog post! See you then…
The other parts:
Recap:
- Commissioning the bass: How I decided what to do
- Part 1: Choosing the components
- Part 2: Early progress - the shapes emerge
- Part 3: Ferdinand works the wood.
The Bass Emerges...
Continuing the sequence, we see the face emerge from the clamps...
The Inlay
My original plan for my input to the bass was to have a single celtic knot band at the 12th fret: we keep markers along the top, and the board itself is unmarked apart from the 12th fret. I found some great designs, including these -
I figured something around the middle of that picture would be good: done in abalone, with a bit of sparkle. Ferdinand agreed, and I sent the URL of the site across. We worked through this early on, just after settling on the materials for the build.
The build progressed nicely: we got to this stage:

And I was getting pretty excited: but then.... argh! The inlays are delayed, so we have to come up with a rapid solution (this happened a week ago last Saturday: with 2 weeks to go!!!)... so I start looking for images I can use. I measured up a different 5-string with similar spacing, and decided 40 x 15mm seems about right. We have another Facetime session, and Ferdinand tells me he knows some guys who have a computer-controlled CNC machine, and he shows me a selection of abalone which the inlay could be made out of. I'm intrigued about what might be possible, and want to keep the core idea of a celtic band.
I'm searching for celtic bands, and I find things like

which is pretty good. I filled in the shape to see how it might look, white-on-black: it wasn't bad, but still not great. And besides, with my geek hat on, I know the computer CNC guys are going to want something which isn't a JPG - they're going to want a vector format (see, I can geek!).
I hunt around and find this: Now granted, this looks pretty pixelated, but... it's an adobe illustrator file - a vector format! This could be an ideal way to get things moving quickly…

I tell Ferdinand the bottom one is preferable: I didn't twig at the time that it was a pair of infinity signs: it's a nice figure, and it scales to 15x40 well.
Anyway, I hear back from Ferdinand a couple of days later: The CNC guys were able to rout out the shape nicely, and he then engraved the piece and added black lines to give it the 3-D over/under look - and see the result!

... and when the light hits it right!!!

And after the fretting over the inlay...
And finally - she's got a full set of stainless steel frets!

These are a little more expensive - Ferdinand tells me he uses an entire set of files because they're so hard: this is exactly why I wanted to specify the materials though, longevity and a trouble-free bass!
I did a little editing on my iPad to make a backdrop out of it - you can really see the beautiful work here: the CNC guys made a fine piece, and Ferdinand's engraving has absolutely made the inlay: it's just stunning!

Finally... where the controls go?
This last show is the latest one I've got: I've seen her in one last facetime session, last friday, where Jacco (the God of Wiring, tremble in his Mighty Presence!) and I discussed how the controls would work: a great chat, where the flexibility of tone was paramount - I'm going for the switchbucker pickups, so I want to be able to get as many tones as possible. The recent work I've done on basses with OBP-3 was on basses which were modded, and already had a set layout: this meant stacked pots and blend controls.
Jacco and Ferdinand were kind enough to recommend twin volume pots for the 2 pickups: this bass has a good sized space for 5 controls!
So our final control layout is 2 above, 3 below: we have
- bridge pickup (with push/pull for passive - yay!), neck pickup as 2 separate controls
- bass, mid (with push/pull for the switchable mid on the OBP-3), treble.
That brings us up to date: My next post will be the final build blog post! See you then…
Sunday, March 01, 2015
Rikkers Build, Part 3: Hand-carving the back and neck joint
Background: I've commissioned a bass from Rikkers in Holland - it's proving to be a seamless, easy and fun process (I saved the money up before I ordered, so less worry there!), so I thought it would be cool to document the experience for myself, and anyone else who wants to know what it's like. I can recommend Rikkers - I'm lucky enough to have synchronised the order with the London Bass Guitar Show so I can pick it up at the show - in a week!
Recap:
Lots more good backdrops here... here's how we start out - the machine does a nice job, but the neck heel needs that personal touch :-)

So Ferdinand gets stuck in: Wood mallets and chisels. Nice!

And the rough-hewn shape emerges:

Now he refines things using a tiny hand-plane!

Very nice.

Now - the bodyline back has some great contours in it, which also needs some carving: more work with the chisel. Love the curve on that neck heel - done by eye and gorgeous!



And, of course, we need to level that out a little...


The end result - very nice.

Next time: The Inlay Crisis and Tantalising Shots of the bass!
Recap:
- Commissioning the bass: How I decided what to do
- Part 1: Choosing the components
- Part 2: Early progress - the shapes emerge
The Back of the Bodyline: Hidden, but beautiful
This video shows some of the great work which happens at Rikkers, and it was a real pleasure to get shots of the bass being carved: Ferdinand loves working wood with hand tools, and it shows!Lots more good backdrops here... here's how we start out - the machine does a nice job, but the neck heel needs that personal touch :-)











Rikkers Build, Part 2: Hearing about early progress!
As I type, it's the 1st of March 2015 and I pick up the Bass in a week at the London Bass Guitar Show: I'm documenting the process for posterity, hopefully it might help anyone who thinks about getting a truly custom bass built.
In this post, I discussed how I came to realise I wanted to commission a bass - short story, I fell madly in love with a Rikkers bass at the 2014 LBGS (careful how you type that) and over the year came to realise that if I set my mind to it, I could get the cash together to commission one.
In this post, I detailed how Ferdinand Rikkers (the man himself!) gave me a great experience choosing woods - and the highly-figured Olivewood top which this bass will have.
With enough inputs from me to get going, Ferdinand set about building the bass. I was keen to get plenty of shots: To see the component raw materials converted into the wonderful end result, and the care and attention that goes into the Bass.
The guys have great communication, using Email, iMessage, FaceTime video, regular calls and Facebook messaging - so you're always able to find out what they're up to: and they respond really quickly to incoming messages (we'll see how handy that is in the next installment...)
First, he cut out the top and the ebony for the board. This is a great shot, because it shows the bookmatched olivewood and how it'll contrast with the neck: you can really see the figuring in the top.

I think I got this a couple of days after we decided what the woods would be. As you can imagine, this basically became the desktop backdrop on every machine I have...
Next I got updates showing the neck sandwich!
I like the way you can see the markings on here for the body and headstock:

And bottle jacks are evidently a great way to glue neck laminates :-)

The block's got a headstock! My first chance to see how the neck laminates look - I like the contrast - and you can see the body wings and top together...

Time to glue our wings on. How are we going to fly without wings?

It's a little like an 8-bit pixel version of the curvaceous beast it will become at this point, but the neck heel is emerging! I like this picture as it shows neck angle in comparison to the wings: interesting!
With apologies to the LBGS's facebook campaign ;-) How many clamps? LOTS!

And, of course, we need to glue the ebony on. You can see the curves are emerging!

Next time: The hand-tooling shots (gratuitous use of human faculties for shaping raw materials - very Zen)
In this post, I discussed how I came to realise I wanted to commission a bass - short story, I fell madly in love with a Rikkers bass at the 2014 LBGS (careful how you type that) and over the year came to realise that if I set my mind to it, I could get the cash together to commission one.
In this post, I detailed how Ferdinand Rikkers (the man himself!) gave me a great experience choosing woods - and the highly-figured Olivewood top which this bass will have.
Progress!
With enough inputs from me to get going, Ferdinand set about building the bass. I was keen to get plenty of shots: To see the component raw materials converted into the wonderful end result, and the care and attention that goes into the Bass.
The guys have great communication, using Email, iMessage, FaceTime video, regular calls and Facebook messaging - so you're always able to find out what they're up to: and they respond really quickly to incoming messages (we'll see how handy that is in the next installment...)
First, he cut out the top and the ebony for the board. This is a great shot, because it shows the bookmatched olivewood and how it'll contrast with the neck: you can really see the figuring in the top.

I think I got this a couple of days after we decided what the woods would be. As you can imagine, this basically became the desktop backdrop on every machine I have...
Cut your neck out,,,
Next I got updates showing the neck sandwich!
I like the way you can see the markings on here for the body and headstock:

And bottle jacks are evidently a great way to glue neck laminates :-)

We could use a little body...
The block's got a headstock! My first chance to see how the neck laminates look - I like the contrast - and you can see the body wings and top together...

Time to glue our wings on. How are we going to fly without wings?

It's a little like an 8-bit pixel version of the curvaceous beast it will become at this point, but the neck heel is emerging! I like this picture as it shows neck angle in comparison to the wings: interesting!
Giving it some BassFace
With apologies to the LBGS's facebook campaign ;-) How many clamps? LOTS!

And, of course, we need to glue the ebony on. You can see the curves are emerging!

Next time: The hand-tooling shots (gratuitous use of human faculties for shaping raw materials - very Zen)
Subscribe to:
Posts (Atom)