I've recently completely cleared out the studio and found my fake books: I'm not a huge jazz fan, but the complexity of the music (in comparison to other styles) and the way the books are laid out (just melody and chords) is a great study tool for "knowing the chords".
Historically theory isn't my strong suit: I remember a disgusted sax player who couldn't understand why I couldn't play through changes in a more complex song, just by knowing the chords. The truth is, like lot of self-taught players, I've done it all by ear, really: I can learn basslines from the dots but I don't have a cerebral grounding in chord theory and knowing the language, so to speak.
I plan to start stretching myself in this department. Today I just started with a youtube video of a backing for Donna Lee at http://youtu.be/fVOTUXfqhhE and the fake book entry: Listening to the backing, I know where the song is having learned the Jaco solo: but playing the bassline through the changes? Once again - I'm not fluent, not fluid: I don't yet understand how this is done. I can see a lot of work ahead, and the thing is to break the blank sheet anxiety and get stuck in with the modern resources at hand.
Wish me luck. What are you shedding with?
P.S. Tomorrow is Rikkers pick-up day!! I suspect the bass is currently on the front of the Rikkers stand, where it's picking up some attention :-)
Daily happenings in a UK Bass Player's tiny tiny Gig fuelled world...
Saturday, March 07, 2015
Tuesday, March 03, 2015
Rikkers Build, Part 5: THE FINAL STRETCH….!
Background - I commissioned a custom Olive-faced 5-string bass from Rikkers in Holland - 15 years or so after first considering a custom bass. The experience has been an education, and a great experience (I can recommend Rikkers), so I thought I'd properly document it.
The other parts:
Nice to see the guys sign the bass on the inside as well as showing their quality on the outside!

Getting the pickups fixed in place is an interesting job, and wiring her up (for 18v of wicked overhead via the OBP-3 preamp) takes a while, and needs Jacco the Wiring God and his Goggles of Extreme Precision.
Marvel at his prowess in this video!
The wiring job looks excellent – we’re well screened here. I like the way the twin 9v batteries have their own little compartment: no way to damage electronics if they broke free, because they can’t!

Ferdinand worked his magic on the frets (stainless steel – they need some work, a set of files gets used up!)

And so, we reach the final shots – and my new beauty emerges for her closeups, Mr DeVille.
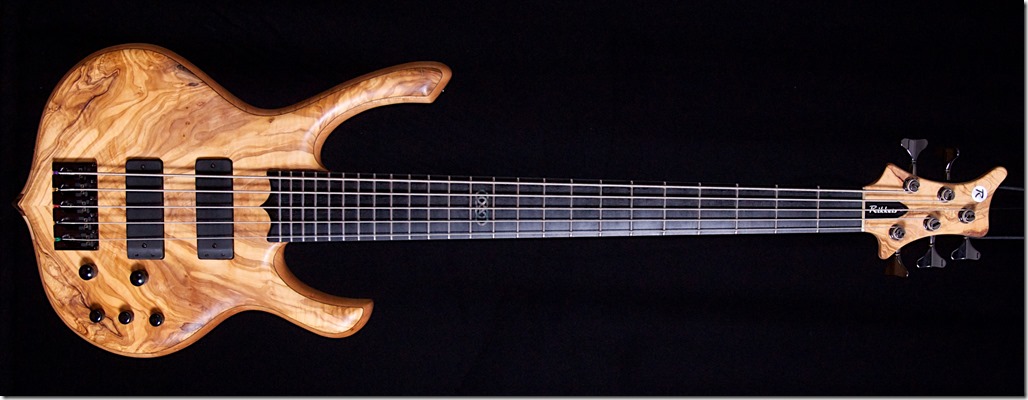

I’m booking the train tickets for Sunday TONIGHT!
The other parts:
- Commissioning the bass: How I decided what to do
- Part 1: Choosing the components
- Part 2: Early progress - the shapes emerge
- Part 3: Ferdinand works the wood.
- Part 4: The bass visualised, and “The Inlay”
Nice to see the guys sign the bass on the inside as well as showing their quality on the outside!
Getting the pickups fixed in place is an interesting job, and wiring her up (for 18v of wicked overhead via the OBP-3 preamp) takes a while, and needs Jacco the Wiring God and his Goggles of Extreme Precision.
Marvel at his prowess in this video!
The wiring job looks excellent – we’re well screened here. I like the way the twin 9v batteries have their own little compartment: no way to damage electronics if they broke free, because they can’t!
Ferdinand worked his magic on the frets (stainless steel – they need some work, a set of files gets used up!)
And so, we reach the final shots – and my new beauty emerges for her closeups, Mr DeVille.
The Bass.
I’m booking the train tickets for Sunday TONIGHT!
Monday, March 02, 2015
Rikkers build, Part 4: The Bass Emerges (and "The Inlay")
Background - I commissioned a custom Olive-faced 5-string bass from Rikkers in Holland - 15 years or so after first considering a custom bass. The experience has been an education, and a great experience (I can recommend Rikkers), so I thought I'd properly document it.
The other parts:
Recap:


I figured something around the middle of that picture would be good: done in abalone, with a bit of sparkle. Ferdinand agreed, and I sent the URL of the site across. We worked through this early on, just after settling on the materials for the build.
The build progressed nicely: we got to this stage:

And I was getting pretty excited: but then.... argh! The inlays are delayed, so we have to come up with a rapid solution (this happened a week ago last Saturday: with 2 weeks to go!!!)... so I start looking for images I can use. I measured up a different 5-string with similar spacing, and decided 40 x 15mm seems about right. We have another Facetime session, and Ferdinand tells me he knows some guys who have a computer-controlled CNC machine, and he shows me a selection of abalone which the inlay could be made out of. I'm intrigued about what might be possible, and want to keep the core idea of a celtic band.
I'm searching for celtic bands, and I find things like

which is pretty good. I filled in the shape to see how it might look, white-on-black: it wasn't bad, but still not great. And besides, with my geek hat on, I know the computer CNC guys are going to want something which isn't a JPG - they're going to want a vector format (see, I can geek!).
I hunt around and find this: Now granted, this looks pretty pixelated, but... it's an adobe illustrator file - a vector format! This could be an ideal way to get things moving quickly…

I tell Ferdinand the bottom one is preferable: I didn't twig at the time that it was a pair of infinity signs: it's a nice figure, and it scales to 15x40 well.
Anyway, I hear back from Ferdinand a couple of days later: The CNC guys were able to rout out the shape nicely, and he then engraved the piece and added black lines to give it the 3-D over/under look - and see the result!

... and when the light hits it right!!!

And finally - she's got a full set of stainless steel frets!

These are a little more expensive - Ferdinand tells me he uses an entire set of files because they're so hard: this is exactly why I wanted to specify the materials though, longevity and a trouble-free bass!
I did a little editing on my iPad to make a backdrop out of it - you can really see the beautiful work here: the CNC guys made a fine piece, and Ferdinand's engraving has absolutely made the inlay: it's just stunning!

This last show is the latest one I've got: I've seen her in one last facetime session, last friday, where Jacco (the God of Wiring, tremble in his Mighty Presence!) and I discussed how the controls would work: a great chat, where the flexibility of tone was paramount - I'm going for the switchbucker pickups, so I want to be able to get as many tones as possible. The recent work I've done on basses with OBP-3 was on basses which were modded, and already had a set layout: this meant stacked pots and blend controls.
Jacco and Ferdinand were kind enough to recommend twin volume pots for the 2 pickups: this bass has a good sized space for 5 controls!
So our final control layout is 2 above, 3 below: we have
- bridge pickup (with push/pull for passive - yay!), neck pickup as 2 separate controls
- bass, mid (with push/pull for the switchable mid on the OBP-3), treble.
That brings us up to date: My next post will be the final build blog post! See you then…
The other parts:
Recap:
- Commissioning the bass: How I decided what to do
- Part 1: Choosing the components
- Part 2: Early progress - the shapes emerge
- Part 3: Ferdinand works the wood.
The Bass Emerges...
Continuing the sequence, we see the face emerge from the clamps...
The Inlay
My original plan for my input to the bass was to have a single celtic knot band at the 12th fret: we keep markers along the top, and the board itself is unmarked apart from the 12th fret. I found some great designs, including these -
I figured something around the middle of that picture would be good: done in abalone, with a bit of sparkle. Ferdinand agreed, and I sent the URL of the site across. We worked through this early on, just after settling on the materials for the build.
The build progressed nicely: we got to this stage:

And I was getting pretty excited: but then.... argh! The inlays are delayed, so we have to come up with a rapid solution (this happened a week ago last Saturday: with 2 weeks to go!!!)... so I start looking for images I can use. I measured up a different 5-string with similar spacing, and decided 40 x 15mm seems about right. We have another Facetime session, and Ferdinand tells me he knows some guys who have a computer-controlled CNC machine, and he shows me a selection of abalone which the inlay could be made out of. I'm intrigued about what might be possible, and want to keep the core idea of a celtic band.
I'm searching for celtic bands, and I find things like

which is pretty good. I filled in the shape to see how it might look, white-on-black: it wasn't bad, but still not great. And besides, with my geek hat on, I know the computer CNC guys are going to want something which isn't a JPG - they're going to want a vector format (see, I can geek!).
I hunt around and find this: Now granted, this looks pretty pixelated, but... it's an adobe illustrator file - a vector format! This could be an ideal way to get things moving quickly…

I tell Ferdinand the bottom one is preferable: I didn't twig at the time that it was a pair of infinity signs: it's a nice figure, and it scales to 15x40 well.
Anyway, I hear back from Ferdinand a couple of days later: The CNC guys were able to rout out the shape nicely, and he then engraved the piece and added black lines to give it the 3-D over/under look - and see the result!

... and when the light hits it right!!!

And after the fretting over the inlay...
And finally - she's got a full set of stainless steel frets!

These are a little more expensive - Ferdinand tells me he uses an entire set of files because they're so hard: this is exactly why I wanted to specify the materials though, longevity and a trouble-free bass!
I did a little editing on my iPad to make a backdrop out of it - you can really see the beautiful work here: the CNC guys made a fine piece, and Ferdinand's engraving has absolutely made the inlay: it's just stunning!

Finally... where the controls go?
This last show is the latest one I've got: I've seen her in one last facetime session, last friday, where Jacco (the God of Wiring, tremble in his Mighty Presence!) and I discussed how the controls would work: a great chat, where the flexibility of tone was paramount - I'm going for the switchbucker pickups, so I want to be able to get as many tones as possible. The recent work I've done on basses with OBP-3 was on basses which were modded, and already had a set layout: this meant stacked pots and blend controls.
Jacco and Ferdinand were kind enough to recommend twin volume pots for the 2 pickups: this bass has a good sized space for 5 controls!
So our final control layout is 2 above, 3 below: we have
- bridge pickup (with push/pull for passive - yay!), neck pickup as 2 separate controls
- bass, mid (with push/pull for the switchable mid on the OBP-3), treble.
That brings us up to date: My next post will be the final build blog post! See you then…
Sunday, March 01, 2015
Rikkers Build, Part 3: Hand-carving the back and neck joint
Background: I've commissioned a bass from Rikkers in Holland - it's proving to be a seamless, easy and fun process (I saved the money up before I ordered, so less worry there!), so I thought it would be cool to document the experience for myself, and anyone else who wants to know what it's like. I can recommend Rikkers - I'm lucky enough to have synchronised the order with the London Bass Guitar Show so I can pick it up at the show - in a week!
Recap:
Lots more good backdrops here... here's how we start out - the machine does a nice job, but the neck heel needs that personal touch :-)

So Ferdinand gets stuck in: Wood mallets and chisels. Nice!

And the rough-hewn shape emerges:

Now he refines things using a tiny hand-plane!

Very nice.

Now - the bodyline back has some great contours in it, which also needs some carving: more work with the chisel. Love the curve on that neck heel - done by eye and gorgeous!



And, of course, we need to level that out a little...


The end result - very nice.

Next time: The Inlay Crisis and Tantalising Shots of the bass!
Recap:
- Commissioning the bass: How I decided what to do
- Part 1: Choosing the components
- Part 2: Early progress - the shapes emerge
The Back of the Bodyline: Hidden, but beautiful
This video shows some of the great work which happens at Rikkers, and it was a real pleasure to get shots of the bass being carved: Ferdinand loves working wood with hand tools, and it shows!Lots more good backdrops here... here's how we start out - the machine does a nice job, but the neck heel needs that personal touch :-)











Rikkers Build, Part 2: Hearing about early progress!
As I type, it's the 1st of March 2015 and I pick up the Bass in a week at the London Bass Guitar Show: I'm documenting the process for posterity, hopefully it might help anyone who thinks about getting a truly custom bass built.
In this post, I discussed how I came to realise I wanted to commission a bass - short story, I fell madly in love with a Rikkers bass at the 2014 LBGS (careful how you type that) and over the year came to realise that if I set my mind to it, I could get the cash together to commission one.
In this post, I detailed how Ferdinand Rikkers (the man himself!) gave me a great experience choosing woods - and the highly-figured Olivewood top which this bass will have.
With enough inputs from me to get going, Ferdinand set about building the bass. I was keen to get plenty of shots: To see the component raw materials converted into the wonderful end result, and the care and attention that goes into the Bass.
The guys have great communication, using Email, iMessage, FaceTime video, regular calls and Facebook messaging - so you're always able to find out what they're up to: and they respond really quickly to incoming messages (we'll see how handy that is in the next installment...)
First, he cut out the top and the ebony for the board. This is a great shot, because it shows the bookmatched olivewood and how it'll contrast with the neck: you can really see the figuring in the top.

I think I got this a couple of days after we decided what the woods would be. As you can imagine, this basically became the desktop backdrop on every machine I have...
Next I got updates showing the neck sandwich!
I like the way you can see the markings on here for the body and headstock:

And bottle jacks are evidently a great way to glue neck laminates :-)

The block's got a headstock! My first chance to see how the neck laminates look - I like the contrast - and you can see the body wings and top together...

Time to glue our wings on. How are we going to fly without wings?

It's a little like an 8-bit pixel version of the curvaceous beast it will become at this point, but the neck heel is emerging! I like this picture as it shows neck angle in comparison to the wings: interesting!
With apologies to the LBGS's facebook campaign ;-) How many clamps? LOTS!

And, of course, we need to glue the ebony on. You can see the curves are emerging!

Next time: The hand-tooling shots (gratuitous use of human faculties for shaping raw materials - very Zen)
In this post, I discussed how I came to realise I wanted to commission a bass - short story, I fell madly in love with a Rikkers bass at the 2014 LBGS (careful how you type that) and over the year came to realise that if I set my mind to it, I could get the cash together to commission one.
In this post, I detailed how Ferdinand Rikkers (the man himself!) gave me a great experience choosing woods - and the highly-figured Olivewood top which this bass will have.
Progress!
With enough inputs from me to get going, Ferdinand set about building the bass. I was keen to get plenty of shots: To see the component raw materials converted into the wonderful end result, and the care and attention that goes into the Bass.
The guys have great communication, using Email, iMessage, FaceTime video, regular calls and Facebook messaging - so you're always able to find out what they're up to: and they respond really quickly to incoming messages (we'll see how handy that is in the next installment...)
First, he cut out the top and the ebony for the board. This is a great shot, because it shows the bookmatched olivewood and how it'll contrast with the neck: you can really see the figuring in the top.

I think I got this a couple of days after we decided what the woods would be. As you can imagine, this basically became the desktop backdrop on every machine I have...
Cut your neck out,,,
Next I got updates showing the neck sandwich!
I like the way you can see the markings on here for the body and headstock:

And bottle jacks are evidently a great way to glue neck laminates :-)

We could use a little body...
The block's got a headstock! My first chance to see how the neck laminates look - I like the contrast - and you can see the body wings and top together...

Time to glue our wings on. How are we going to fly without wings?

It's a little like an 8-bit pixel version of the curvaceous beast it will become at this point, but the neck heel is emerging! I like this picture as it shows neck angle in comparison to the wings: interesting!
Giving it some BassFace
With apologies to the LBGS's facebook campaign ;-) How many clamps? LOTS!

And, of course, we need to glue the ebony on. You can see the curves are emerging!

Next time: The hand-tooling shots (gratuitous use of human faculties for shaping raw materials - very Zen)
Saturday, February 28, 2015
Rikkers Build, Part 1: Choosing the components
A little background first - after some great success modifying basses (and having them modified) and trying one of their olive-topped 5 strings at the london bass guitar show 2014, I decided to get a similar bass built by Rikkers (based in Holland - http://http://www.rikkersgitaarbouw.nl).
Rikkers go into great detail and apply great craft to their instruments, hand-winding their own pickups - their SwitchBucker units have a great USP - microswitches on the individual coils for superb tonal flexibility. Ferdinand has been making basses for 30 years, and his entire demeanour speaks of a quiet inner satisfaction in the work he does. He's a happy man.
So, it was with great anticipation I entered into the design phase of the project! Rikkers being in Holland, the guys decided to use facetime and general Apple-y tech goodness to consult: I'd already decided that I wanted the Bodyline - which I suspect is amongst the first shapes Ferdinand made when he started out. It's a great looking bass, balanced with a nice taper at the bridge and a great headstock shape. First order of business though, choosing the olive top!
With enthusiasm and patience, Ferdinand showed me a huge hunk of Olive he has (part of a diminishing stock, apparently!) and proceeded to use a black outline of half the bass and a mirror (neat!) to show me potential tops: the eventual outcome would look slightly different as the wood is cut and then bookmatched.
Here's what I had to choose from:
I liked this one, it has lots of interest and a sweeping curve from the bridge end to the horns:

Ferdinand thought this one would be fun - it's got a frog in it!

This one reminded me of zebras:

And this one has very strong lines with interest on the wings:

Another interesting combination of shapes here - the bass almost has a sort of rounded triangular shape on it.

After some deliberation for a couple of days, I went with my gut instinct: the first one! The combination of sweeping curves in a V, combined with the interesting shapes on the wing pieces, had a Quality about it which drew me to it: I'm a strong believer that your initial instincts are often the best ones, particularly in visual stuff.
Then we settled on materials for the rest of the build: I wanted a "nathan east" style sound - something modern, focussed, with plenty of scope for tonal variation (the OBP-3 Rikkers uses gives a lot here) - Ferdinand had great suggestions, and I did some research via some guitar builder websites: there's some excellent material out there on tonewoods and the kind of attack, decay etc they will give your sound. The bass is a through-neck, so the wings don't contribute a huge amount to the sound: the neck woods are the engine here. After reading about how ebony fingerboards help give a focussed tone, I decided on that (tips from Mr East there) - but what to do for the neck?
After some discussion, we went with a 5-piece laminate of hard maple, Ovangkol and Wenge: the headstock gets faced with another slice of that glorious olive wood.
We go for black hardware (I like the contrast) and top dot-markers on the edge of the board, but only one inlay on the front of the fingerboard: I wanted to have a single statement input into the bass. I decided to put some kind of celtic knot band at the 12th fret, in abalone so it would shine in the darkness of the ebony.
Frets are stainless steel (I hadn't realised you could make frets in stainless steel!) - a little extra as dressing them actually wears out a set of files! But the longevity will be a great thing: apparently the frets wear out strings, which is great.
In terms of playability, I went for a wide spacing: this bass is to be an all-rounder, with a leaning towards ease of thumb-work for funk!
All these items were discussed with the kind of open, friendly chat you'd want: gentle recommendations, agreement on good ideas: an exciting and engaging process!
Rikkers take 25% up front, with the balance before delivery: in my case, this worked really well as I wanted to pick the bass up at the bass guitar show - and kicking the build off in time was crucial.
Next time: How the build progressed, and the updates I got while it was happening!
Rikkers go into great detail and apply great craft to their instruments, hand-winding their own pickups - their SwitchBucker units have a great USP - microswitches on the individual coils for superb tonal flexibility. Ferdinand has been making basses for 30 years, and his entire demeanour speaks of a quiet inner satisfaction in the work he does. He's a happy man.
So, it was with great anticipation I entered into the design phase of the project! Rikkers being in Holland, the guys decided to use facetime and general Apple-y tech goodness to consult: I'd already decided that I wanted the Bodyline - which I suspect is amongst the first shapes Ferdinand made when he started out. It's a great looking bass, balanced with a nice taper at the bridge and a great headstock shape. First order of business though, choosing the olive top!
Choosing the top
With enthusiasm and patience, Ferdinand showed me a huge hunk of Olive he has (part of a diminishing stock, apparently!) and proceeded to use a black outline of half the bass and a mirror (neat!) to show me potential tops: the eventual outcome would look slightly different as the wood is cut and then bookmatched.
Here's what I had to choose from:
I liked this one, it has lots of interest and a sweeping curve from the bridge end to the horns:

Ferdinand thought this one would be fun - it's got a frog in it!

This one reminded me of zebras:

And this one has very strong lines with interest on the wings:

Another interesting combination of shapes here - the bass almost has a sort of rounded triangular shape on it.

After some deliberation for a couple of days, I went with my gut instinct: the first one! The combination of sweeping curves in a V, combined with the interesting shapes on the wing pieces, had a Quality about it which drew me to it: I'm a strong believer that your initial instincts are often the best ones, particularly in visual stuff.
Neck and Wings...
Then we settled on materials for the rest of the build: I wanted a "nathan east" style sound - something modern, focussed, with plenty of scope for tonal variation (the OBP-3 Rikkers uses gives a lot here) - Ferdinand had great suggestions, and I did some research via some guitar builder websites: there's some excellent material out there on tonewoods and the kind of attack, decay etc they will give your sound. The bass is a through-neck, so the wings don't contribute a huge amount to the sound: the neck woods are the engine here. After reading about how ebony fingerboards help give a focussed tone, I decided on that (tips from Mr East there) - but what to do for the neck?
After some discussion, we went with a 5-piece laminate of hard maple, Ovangkol and Wenge: the headstock gets faced with another slice of that glorious olive wood.
Hardware and little touches...
We go for black hardware (I like the contrast) and top dot-markers on the edge of the board, but only one inlay on the front of the fingerboard: I wanted to have a single statement input into the bass. I decided to put some kind of celtic knot band at the 12th fret, in abalone so it would shine in the darkness of the ebony.
Frets are stainless steel (I hadn't realised you could make frets in stainless steel!) - a little extra as dressing them actually wears out a set of files! But the longevity will be a great thing: apparently the frets wear out strings, which is great.
In terms of playability, I went for a wide spacing: this bass is to be an all-rounder, with a leaning towards ease of thumb-work for funk!
All these items were discussed with the kind of open, friendly chat you'd want: gentle recommendations, agreement on good ideas: an exciting and engaging process!
How you pay
Rikkers take 25% up front, with the balance before delivery: in my case, this worked really well as I wanted to pick the bass up at the bass guitar show - and kicking the build off in time was crucial.
Next time: How the build progressed, and the updates I got while it was happening!
Tuesday, January 27, 2015
Commissioning a Bass: Engaging with a builder.
I thought it might be nice to write this one up, and I'll start from the beginning. Remember, this is a personal story: yours might be radically different. But if anything, it proves that some old adages are true...
Background: I've been modding basses recently...
If you take a look at some of the earlier posts here, you'll see I've been tinkering with the basses I already have:
- Tobias Toby Pro-6 - got a local luthier to fit an OBP-3 and GK-3B mini pickup kit (nice job, too)
- Hohner B-Bass V - fitted an OBP-3 myself (good fun)
- Self-assembly fretless (OK, the body is an Allparts one from someone else's project and it's already loaded... but hey) - giving a beautiful neck a better home
I enjoyed the mods I did, and I've been thinking about why I was tinkering: I've got some great basses, and I think the sonic deficiencies (and in the case of the poor Tobias, the bloody great strap-on bracket with a full-on GK-3B strapped to it) eventually showed themselves.
Maybe 10 years ago, I considered purchasing a Sei bass - their basses are just beautiful - but the ones I had always fitted what I needed to do (and I didn't have the resources to commission one). I think additionally I didn't have an appreciation back then for the different sounds which woods and electronics bring to a bass - I've now got passive Japanese basses, active Warwicks, the Tobias - and the recent quest to upgrade these opened my eyes to the potential of a truly "personal" bass from a luthier.
The London Bass Show 2014
Checking bas to the abbreviated post I made about it, and remembering (it's a diary, after all) I recall being very impressed by several bass manufacturers - Eve from Scotland make lovely basses, also caught sight of some of the exotica on sale from the US, but ultimately I appear to have fallen for Rikkers - and a particular bass too, their Olive top bodyline:
"tried out a Rikker bass, an utterly stunning olive top 5 string fretless with Piezo in individual bridge saddles - gorgeous tone, setup perfect, ~£2100 worth if heaven! Turns out it uses the same Aguilar OBP-3 as I'm having fitted into the Tobias, so I'm hopeful the boost and control will give me something great. The Rikkers guys talked with me for more than half an hour on the Metaphysics of Quality and how they make the guitars: they wind their own pickups, meditate and use Zen breathing, I love their approach. The basses just ooze the results of it. I will be saving up for one."
I remember walking around the show, drinking in amps (I took a Warwick with me), enjoying sitting down with a few custom made basses and playing some different styles, trying pickup combinations and tone settings.
But I really remember that olive top bass: the attention to detail, the story of how they fit the microswitches into the pickups on their switchbuckers (an inspired idea), the excellent detailing on the bass, the solidness of it: I wished I'd had more time to explore it in more detail: the grain of the wood was stunning, and it wasn't a lacquer top: I love waxing basses to clean them: oil and wax gives a feel from the moment you pick up the bass: before you strap it on, it already tells you something from that touch.
Their calm, happy stand actually felt like an oasis (apart from when some guy spent 15 minutes cranking out the worst slap I've ever heard on a P-bass!) - I spent 10 mins just watching the video of them using hand tools, and wrapping wire for pickups.
The upshot.
Around September / October / November 2014, I worked hard to accumulate some cash and decided I had enough to commission a bass: I had no problem deciding where to go - as much as the bass itself, the approach taken by the Rikkers guys just oozed attention to detail. So I got in touch with them and we set up a meeting to talk about what was possible...Next time, I'll talk about what we talked about. Until then!
Funny thing - I grabbed brochures from other places, but the only "selfie" from the show is me, with that olive top bass.
Subscribe to:
Posts (Atom)